How to Solve Material Flow in 10 Common Processing Vessels
Comments Off on How to Solve Material Flow in 10 Common Processing Vessels5 Food Industry Trends for 2025
Comments Off on 5 Food Industry Trends for 2025The food processing industry has undergoing significant transformations, driven by factors such as changing consumer preferences, technological advancements, economic conditions, regulatory policies, and environmental concerns. Learn about food industry trends that can affect plant operations and production goals.
1. Green Food Processing
Sustainability is no longer a buzzword; it’s a mandate. Consumers and regulators alike demand eco-friendly practices that minimize environmental impact. This shift compels manufacturers to adopt renewable energy sources, reduce waste, and implement sustainable methods throughout production. Embracing green food processing not only meets regulatory requirements but also appeals to the growing segment of eco-conscious consumers.
2. Food Waste Management
With global food waste contributing significantly to environmental degradation, the industry is under pressure to enhance resource utilization. Innovations in processing techniques and supply chain management are being developed to address this issue. Efficient utilization of resources, improved storage solutions, and advanced inventory management systems are among the strategies employed to minimize waste. By tackling food waste, manufacturers can enhance profitability and contribute to food security.
Flow aids can help minimize material waste caused by inconsistent flow. A food company threw away 40 pounds of mixture a day, and even had to pay to have it hauled away, until they installed AirSweep. Watch how AirSweep can be used to promote first-in/first-out flow for all types of food materials.
3. Alternative Proteins
The rise of plant-based and lab-grown proteins is transforming the food landscape. These alternatives cater to health-conscious consumers and address environmental concerns associated with traditional meat production. Incorporating alternative proteins into product lines allows manufacturers to diversify offerings and meet the evolving preferences of consumers seeking sustainable and ethical food choices.
4. Enhanced Food Safety Measures
Advancements in technology are leading to improved food safety protocols. The implementation of early warning systems, real-time analytics, and AI-driven solutions helps in the proactive detection and prevention of foodborne illnesses. By prioritizing food safety, manufacturers can protect public health, comply with stringent regulations, and maintain consumer trust.
5. Personalized Nutrition
With the rise of personalized nutrition, food safety is becoming more tailored to individual dietary needs. Technologies that track dietary preferences, allergens, and nutritional requirements are driving the development of personalized food products. This trend enables manufacturers to offer customized solutions, enhancing customer satisfaction and opening new market opportunities.
Keep up with Food Industry Trends with a Smarter Flow Aid
AirSweep can help food manufacturers align with industry trends such as sustainability, waste reduction, and enhanced food safety. The system’s efficiency contributes to greener processing by minimizing material waste and reducing energy consumption associated with manual cleaning and maintenance. It also provides consistent and powerful material flow, even for challenging materials like alternative protein products. Find out more about how AirSweep is used in the food industry and why it is more effective than other flow aids.
7 Most Common Bulk Materials Prone to Bridging and Ratholing
Comments Off on 7 Most Common Bulk Materials Prone to Bridging and RatholingBridging and ratholing are common problems in bulk material handling, and some materials are notorious for poor flow properties. Learn about the most challenging bulk materials and see proof of why AirSweep is the best flow aid for the job.
What are bridging and ratholing?
Bridging happens when bulk materials form a stable arch above an outlet, completely stopping the flow. This usually occurs because of particle cohesion, moisture, or poor hopper design.
Ratholing creates a narrow channel through the material, leaving stagnant product clinging to the container walls. It’s common with materials that have poor flow properties or stick easily to surfaces.
Both problems cause production stoppages, material spoilage, and costly manual intervention—headaches no plant manager wants.
What materials are prone to bridging and ratholing?
Flow problems can be caused by many factors, including vessel design or plant environment (like humidity and temperature). However, these materials have inherent properties that affect how they behave when they are stored, transported, or mixed.
1. Cement and Fly Ash
Cement and fly ash are ultra-fine powders that easily absorb moisture. This leads to clumping, compacting, and cohesion that quickly cause bridging. When stored under pressure, these materials become even tougher to handle because the pressure forces particles closer together, increasing their density and cohesion. The compacted material can form stable arches or stick tightly to hopper walls, making flow nearly impossible without external intervention.
Watch: AirSweep Cement Mix Material Flow Test
2. Food Powders
Most food or beverage processing facilities or commercial bakeries use fine powders like flour, cornstarch, cocoa, and milk powder. These powders are hygroscopic, or readily absorb moisture from the air. Flour and starch compact under their own weight, while cocoa and milk powder stick to hopper walls due to moisture or static charges. These properties make bridging and ratholing and bridging frequent problems.
Food and beverage manufacturers also have to meet strict sanitation standards. Stagnant material can become spoiled, and manually clearing out material blocks may cause contamination.
Watch: AirSweep Moist Cornstarch Material Flow Test
3. Chemicals and Fertilizers
Many chemicals and fertilizers absorb moisture, leading to cohesion and clumping. Granular fertilizers often bridge because of uneven particle sizes, while fine chemical powders compact or stick to equipment surfaces.
Aside from slowing down operations, flow interruptions in fertilizers and chemicals disrupt batching accuracy and downstream processes like mixing and packaging.
4. Plastic Pellets and Resins
Plastic pellets and resins used in plastic production and packaging pose unique challenges. Smooth, spherical pellets interlock under pressure, causing bridging. Irregularly shaped compact and form stable arches in hoppers.
Recycled plastic and resins also pose more challenges. They have varying particle sizes and shapes, increasing the chances of bridging and compacting. As “green manufacturing” becomes a bigger priority because of sustainability goals, reliable flow systems ensure that recycling operations remain efficient, sustainable, and cost-effective.
Watch: AirSweep Plastic Regrind Material Flow Test
5. Coal and Aggregates
Coal and aggregates are typically used in energy production, mining, and construction. These materials often have irregular particle sizes and varying moisture content. Fine coal dust, in particular, sticks together due to cohesion and compaction. Material blocks can choke boiler feed lines and delay energy production—a costly problem for any plant.
6. Metal powders
Metal powders are extremely fine, dense, and prone to static charge buildup. These properties cause bridging, compaction, and ratholing, particularly in precision processes like additive manufacturing.
7. Sawdust and Wood Chips
Sawdust and wood chips are typically used in paper and pulp industries, wood processing, and biomass energy production. They are lightweight and irregularly shaped, which makes them prone to interlocking and bridging in hoppers and silos. Their fibrous nature also causes the material to compress and compact over time, creating blockages that restrict flow.
Watch: AirSweep Sawdust Material Flow Test
Solve bridging and ratholing for good
Do you work with a tough material that is prone to bridging and ratholing? Have you tried other flow aids but still resort to manual cleaning or hammering the vessel? AirSweep provides a proven solution to keep your materials flowing, eliminate costly disruptions, and maximize productivity. To learn how AirSweep can improve your plant’s operations, contact us for a consultation.
How to Solve Bridging and Ratholing of Cement and Mined Materials
Comments Off on How to Solve Bridging and Ratholing of Cement and Mined MaterialsMaterial flow is the backbone of any successful operation in the mining and cement industries. Yet, common issues like bridging, ratholing, and material pileups can derail even the best-laid plans. These disruptions not only impact productivity but also drive up costs with additional labor and energy consumption.
The solution? AirSweep—a proven flow aid trusted by over 10,000 installations worldwide. Designed to handle the heavy-duty challenges of materials like clinker, fly ash, and copper concentrate, AirSweep ensures consistent material flow, minimizes downtime, and keeps operations running smoothly. Read on to discover why AirSweep outperforms traditional flow aids and how it’s revolutionizing bulk material handling in the cement and mining industries.
Common material flow problems in mining and cement
Heavy materials like clinker, fly ash, and copper concentrate pose significant challenges in processing plants. They often:
- Bridge or rathole inside vessels, reducing live capacity.
- Plug outlets, halting production lines.
- Segregate particles, disrupting material quality.
- Flood or flush fine powders, causing inefficiency and waste.
Traditional flow aids like vibrators, air cannons, and fluidizers are no match for such issues. They can compact materials, waste energy, or create safety risks by dispersing particles.
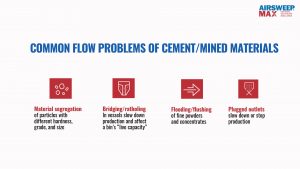
AirSweep flow aids solve the toughest flow problems of cement and mined materials.
Why AirSweep is the best flow aid for cement and mined materials
AirSweep releases high-pressure, high-volume, 360-degree pulses of compressed air that break through material blocks and clear vessel walls. It’s efficient, safe, and designed to tackle the toughest materials. It’s also more efficient, safe, and cost-effective than other flow aids.
- Fluidizers fail to activate heavy materials.
- Air cannons waste energy and spread material dangerously.
- Vibrators compact materials instead of clearing them.
AirSweep, on the other hand, activates materials quickly and completely, using less energy and plant air.
AirSweep is trusted by cement and mining companies worldwide
Built for Durability and Performance
AirSweep systems come with the longest warranty in the business—seven years—a testament to their reliability. Whether you need to clear stubborn clogs in silos or ensure smooth transport in trailers, AirSweep delivers unmatched performance.
Ready to revolutionize your operations? Contact the AirSweep team today to find out how we can optimize your material flow and prevent costly downtime.