Engineers and plant managers are often tasked to design or recommend the right container for storing and handling bulk solids. They have to weigh several factors — capacity, storage duration, installation cost, and how well it protects the material from moisture and pests.
But there’s another factor that greatly affects productivity and can lead to expensive hidden costs: the material flow. Some containers are more prone to bridging and arching, particularly above the discharge. This can affect productivity, product quality, and profit.
Let’s look at the two most common containers – silos and hoppers – and how to promote reliable material flow in them.
Overview: Material flow: How to improve it in silos and hoppers
Silos and hoppers are prone to different material flow issues. In the following slide presentation, you’ll learn the difference between the two and how material flow can help improve their performance.
What’s the difference between a silo and a hopper?
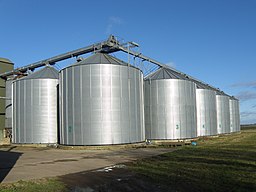
Silos are the oldest storage vessel used by man. Credit: Michael Trolove / Grain Silos at Manor Farm
Silos are used for bulk storage. While the earliest silos were primarily used to store extra grain, modern silos can hold any kind of material: cement, black carbon, plastic resins, wood chips, and more.
Common types include tower silos, bunker silos, and bag silos.
Hoppers are used for temporary storage or measured feeding systems. They come in different shapes: cones, wedges, pyramids, or a combination of these.
Common material flow problems
Ideally, any material in silos and hoppers can be discharged quickly and consistently to prevent production delays or accumulation of stagnant material that can spoil or contaminate the next batch. However, many plant managers are plagued with material blocks in their production line.
Ratholing
Material builds up on the vessel walls, restricting the flow and the vessel’s full storage capacity. When the flow channel empties and material flow ceases, it can form a stable rathole that may collapse and block the opening.
Bridging or arching
Materials interlock or bond together to form an arch above the outlet, blocking any flow. The strength of this arch depends on the cohesive strength and internal friction of the particles. Hammering or blasting with an air cannon can break the arch, but this can overload and damage the vessel.
Segregation
If the vessel is filled with different particle sizes, it’s natural for finer particles to collect at the center of the bin, while coarser particles stick to the slope. The variable, inconsistent material discharge can affect product uniformity.
Factors that affect material flow in silos and hoppers
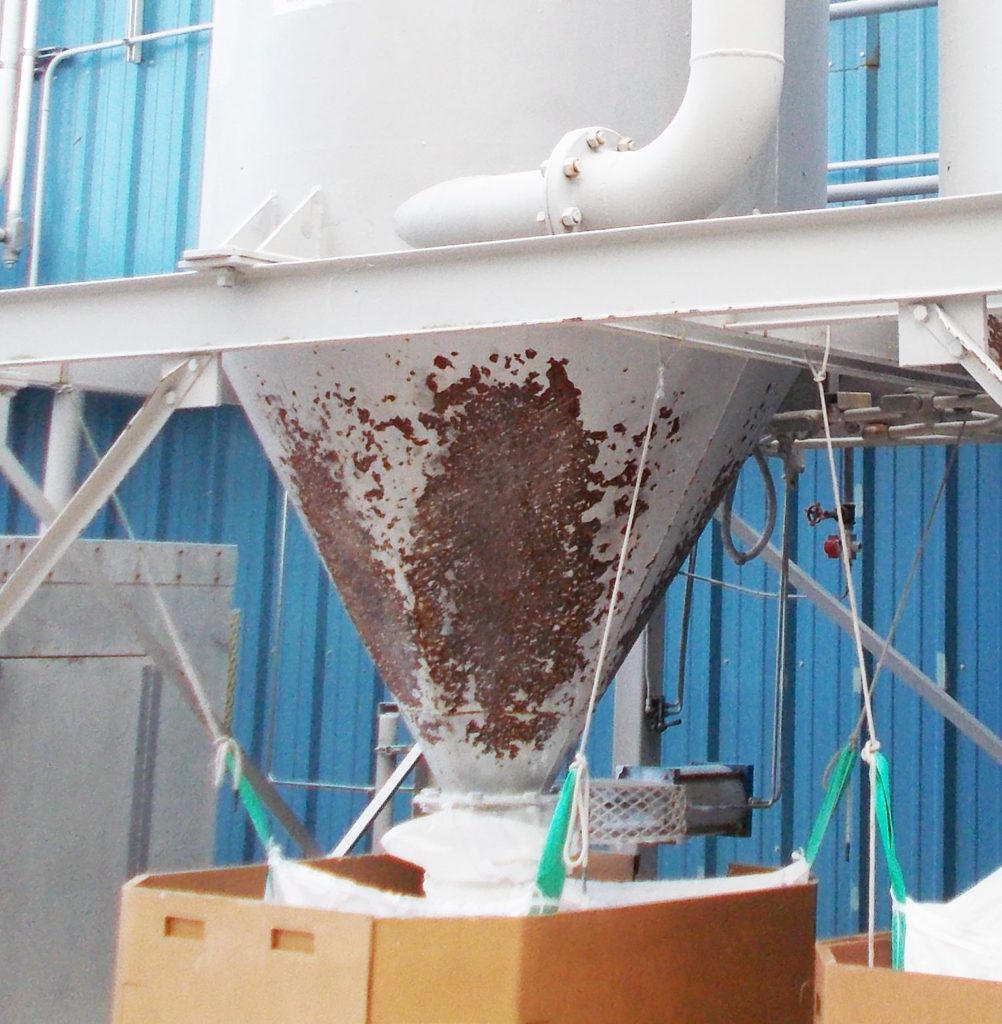
A hopper shows hammer marks from workers who tried to clear material blocks.
Material properties
Some materials are more prone to arching, bridging or segregation. Fine powders, small particles and sticky materials have a higher cohesive strength and tend to bridge or compress along the vessel walls.
Other factors include bulk material density, the pressure applied by its weight in storage, permeability, and tendency to retain moisture. Ideally, these material flow properties are considered while choosing the silo or hopper design.
Vessel angle
If the hopper walls are not steep or smooth enough, the material won’t flow down the vessel walls. It will cake and build up, or if it has enough cohesive strength, it can bridge over the outlet or form a rathole as it empties out.
The hopper angle depends on the friction between the powder and the walls, the friction between powder particles, and the shape of the vessel.
Vessel shape
Generally, square feed hoppers work better for bulk materials with uniform pellets. However, when there is a large variation of particle size — like when virgin material is combined with plastic regrind — circular hoppers allow for a more gradual compression.
Outlet and feeder
The size of the outlet, the discharge rate, and the interface of the feeder can all affect material flow at the bottom of the vessel. This is particularly problematic for materials that have greater cohesive strength and bulk density, or have a tendency to segregate or spoil.
Steep cones or wedge-shaped hoppers may be able to promote mass flow. Flow aids can also break any bridging or arching above the discharge.
How to improve poor material flow in silos and hoppers
Material flow aids can help break through bridging and arching and promote on-demand flow. These can include:
- Mechanical flow aids like vibrators or agitators
- Pneumatic flow aids like fluidizers and AirSweep
- Chemical flow aids like fumed silica
Each flow aid will have its pros and cons. Some are better suited for certain types of bulk solids. For example, vibrators can actually compact moist or dense solids like flax or whey protein, while fluidizers are only effective for light powders like flour. (Get a competitive analysis for different kinds of flow aids.)
Flow aids can be retrofitted into silos and hoppers. This can be more cost-effective than replacing the bins or having them custom-made. Some of them, like the AirSweep, barely require any modification of the silo or the hopper since they are installed on the wall with a mounting bracket.
Finding the “right” flow aid also depends on the type of material, or the size of the silo or hopper. We can provide a customized proposal based on your process.
Contact us to find an affordable and reliable solution to arching, bridging and other material blocks.
Comments are closed