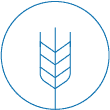
Food/Agriculture
Materials Handled
Animal feeds
Brewer’s grain
Cocoa
Coffee
Corn
Flour
Grains
Hops
Salt
Soybeans
Spices
Starches
Sugar
Fluidizers are a pneumatic flow aid that use a combination of aeration and gentle vibration to promote material flow. The discs force air to move along the vessel wall, which loosens the material and prevents it from plugging or becoming compact.
Fluidizers are often used in storage silos, hoppers, and dust control systems. They can be installed outside or inside the vessel, and are usually made of silicone or EPDM rubber.
Fluidizers work best with dry bulk materials that respond to gentle aeration, or have a moisture content that is less than 12 to 15 percent. There are models designed for either low-pressure/high-volume and high-pressure/low-volume air, but they generally have less power and a smaller activation radius than other flow aids.
Fluidizers are used to prevent ratholing and bridging in silos and other storage containers, or to promote discharge from transportation like dry bulk trailers.
Fluidizers are inexpensive and easy to install, since they only require a small hole for the discs. Some vessels already come with pre-fitted fluidizing systems.
But while the initial costs are low, fluidizers may not be as cost-effective as they seem.
![]() |
Fluidizers |
|
---|---|---|
Functionality | High-pressure, high-volume air pulses lift stalled material back into the flow stream. | Air causes the rubber disks to flap and vibrate, activating material with a combination of gentle vibration and aeration. |
Activation Radius | One nozzle can stimulate up to 2.44m (8 ft.) diameter circle of material | Small, clean radius. You may need to install many units to achieve adequate coverage. |
Maintenance Costs | No damage, vibration, stress or wear to vessel walls
Only needs inspection every 6 months, and replacement of parts after 1,000,000 cycles Uses 10 cfm of compressed air or gas |
May cause vessel wall abrasion
System accessories like hoses, valves, and regulators incur additional hidden costs High energy consumption |
Sanitation | Only the nozzle tip comes in direct contact with material
USDA-accepted models available |
Disc material may degrade, contaminating the product
Not the best solution for food or abrasive materials. |
Worker Safety and Convenience | Reduces workload: can be used to provide on-demand flow or automatic cleaning/flushing of vessels
Parts can be inspected and removed without tools for quick, easy cleaning |
Can present safety issues if workers have to access the inside of the vessel to install or maintain them |
Noise Levels | Makes a quick, ear-friendly “psst” or “pop” | Can be noisy |
Material Control | Effective for all materials, including moist, sticky, and heavy powders and bulk solids | Only effective for light powders like flour |
AirSweep works on almost any kind of material—from fine powders to moist, sticky or wet bulk solids.
Animal feeds
Brewer’s grain
Cocoa
Coffee
Corn
Flour
Grains
Hops
Salt
Soybeans
Spices
Starches
Sugar
Aluminum
Bentonite
Coal
Copper
Diatomaceous earth
Gypsum
Iron ore
Limestone
Magnetite
Phosphate
Shale
Soda ash
Activated carbon
Adipic acid
Aluminum chloride
Boric acid
Chlorine
Herbicide
Hydrated lime
Iron oxide
Polyacrylamide
Titanium dioxide
Zinc
Acetate
Cement
Chalk
Cork
Detergent
Fertilizer
Fly ash
Pharmaceuticals
Plastics
Polymers
Resins sludge
Wax flakes
Wood chips
Many plants that used fluidizers for these materials had to resort to manual cleaning. Eventually, they would shift to more powerful pneumatic flow aids like AirSweep.
An AirSweep® system will pay for itself, in as little as two weeks with:
Control Concepts, Inc. provides a
7-year warranty on the Airsweep® unit.
Copyright Control Concepts, Inc. 2025, 19 S. Main Street, Brooklyn, CT 06234 • ph: 860-928-6551 • fax: 860-928-9450
Notifications