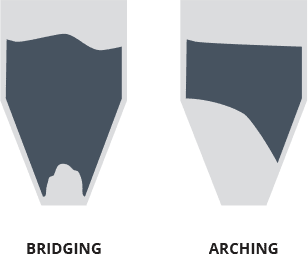
Poor material flow can have a huge impact on a food plant’s quality control, hygiene and sanitation, and overhead costs.
Bridging or arching in a single hopper or silo can compromise an entire batch. Stagnant material can become spoiled. Inconsistent flow affects batch uniformity, and lead to inconsistent flavor and texture.
COMMON MATERIAL FLOW PROBLEMS IN FOOD PRODUCTION

Problematic flow properties
Powders can bind to form a cohesive arch. Flax, cocoa or other materials with a high fat content can cake, or clog pipes or filters.

Plant humidity and temperature
Materials absorb the moisture, and become compact, dense, and difficult to activate.

Contamination
Microorganisms and mold can grow in residue that is left in the vessel or trapped in the flow aid itself.
THE IMPACT OF MATERIAL FLOW ON COST, TIME, AND SAFETY
Material blocks also leave a mess that workers have to clean up—causing delays and other problems that affect your costs and revenues.

MATERIAL WASTE
A flax plant had to throw away 40 pounds of mixture a day, and even had to pay to have it hauled away.
Read More

MANPOWER
A spice manufacturer wasted hours and money every week from manually cleaning ribbon blenders by flushing it with flour.
Read More

WORKPLACE RISK
Bridging from caked whey protein caused a fire in a cheese company’s baghouses.
Read More
AIRSWEEP: PROVEN SOLUTION FOR TOUGH FLOW PROBLEMS
These food companies took control of their material flow problem with the AirSweep® system. AirSweep releases high-pressure, high-volume air pulses that slice through material blocks just like an air knife. Stagnant material is swept back into the flow stream, ensuring first-in/first-out material flow.
AirSweep® is used in the factories of some of the biggest food manufacturers in Asia and North America.
It is proven effective for:
- Animal feeds
- Brewers Grain
- Cocoa
- Coffee
- Corn
- Flour
- Flax
- Grains
- Hops
- Salt
- Soybeans
- Spices
- Starches
- Sugar
- Whey
AIRSWEEP VS OTHER FLOW AIDS
Some flow aids can worsen material blocks or cause more problems than they solve.
“The vibrators that came installed on the bottom of the hopper above the mixture practically turned the flax into concrete. Then we installed fluidizers, which were terrible. We still had to use hammers and sticks, and spent an hour a day to clean and keep things flowing,” says Stanley Rhea, maintenance department head of Flax4Life.
However, AirSweep® was able to solve 90% of their material flow problems. Aside from reducing wastage and improving production speed, they no longer need to climb equipment to dismantle and clean the ingredient receiver.
DESIGNED FOR FOOD SAFETY AND SANITARY PROCESSES
AirSweep’s USDA-accepted models are specially designed to meet the highest standards of sanitation and hygiene.
- Airtight nozzle prevents material retention and bacterial growth
- Modular construction for easy cleaning and inspection
- Tri-flange mount for tool-less removal
PREVENT MATERIAL PILE-UP WITH DAZIC
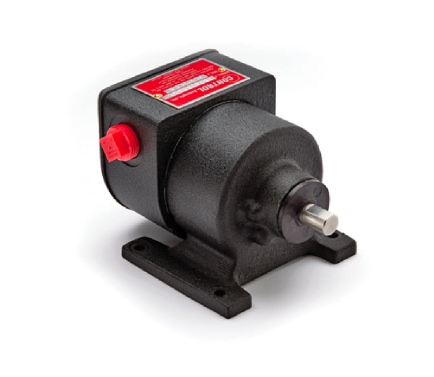
Dazic’s electromechanical, electronic and inductive proximity speed switches can let you know if equipment is running too fast, too slow, or not at all.
Dazic Speed Switches are ideal for any equipment that’s part of a conveyor system or other shaft-driven process components. It can be interlocked into your system to stop operations when a machine slows down, stops, or deviates from standard operating parameters.
PREVENT BUILD-UP AND CONTAMINATION WITH ACOUSTICLEAN
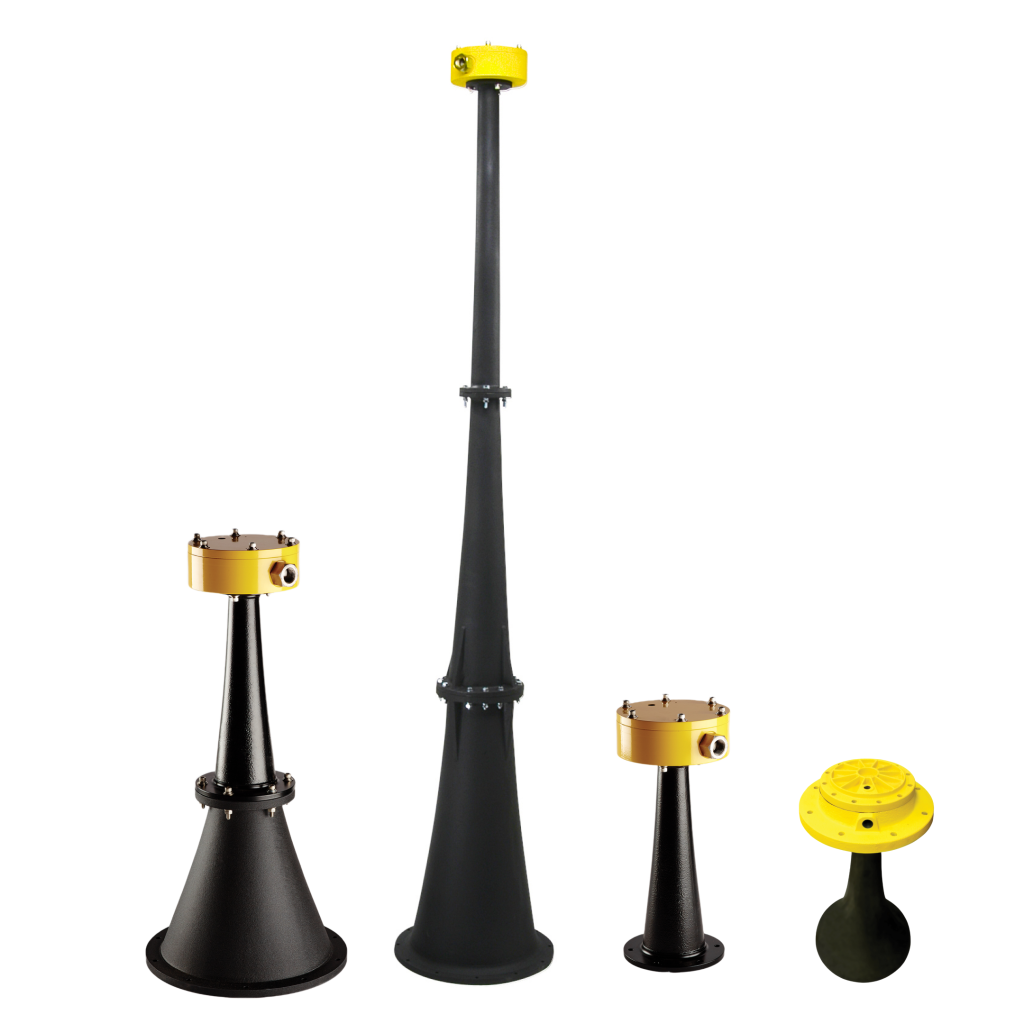
Fine powders like flour can coat the vessel walls, or enter the air ducts. It can contaminate the rest of the process and affects air quality and worker comfort and safety. It can also affect the heat retention and temperature of some equipment, which can affect the process and cause long-term damage.
AcoustiClean® can help prevent the build-up of powders and other particulate matter from accumulating on vessels.
AcoustiClean Sonic Horns produce high-energy, low-frequency sound vibrations that disperse dry material. Compressed air is applied to a sound generator, which vibrates a titanium diaphragm. The sound waves clear the material, to clean your equipment.
- Does not need to use detergents or other cleaning solutions that can contaminate material
- Prevents shutdowns from blocks
- Replaces time-consuming and dangerous cleaning routines
- Increases energy efficiency
- Minimizes long-term damage to equipment
TAKE CONTROL OF YOUR PROCESS
AirSweep®, AcoustiClean® and DAZIC® can be integrated into different parts of your plant to increase efficiency and minimize cost.